Unleash Your Professional Power
Every Course Opens Doors for New Opportunities
Build a Strong Profile With Bakkah
35600
Professionals
2500
Sessions
270
Courses
420
B2B Clients
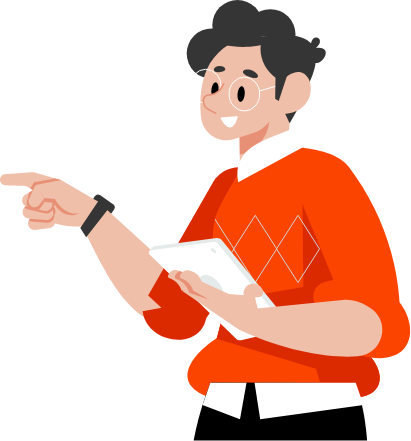
Top Demanded Programs in one Place
A whole professional package!
Our development team has been working around the clock to browse the market and conclude the most
wanted professional courses.
You’re not the Only Astray Professional Soul!
We have sorted things out for you!
Our training plan is thorough yet clear, with the assistance of certified instructors, content designed by professionals, a library of exam simulators, you’ll defiantly pass the actual exam with flying colors, and become the next certified professional!
View MoreStart Learning for Free
You are one click away from hearing about your favorite business topic from an expert
Interactive sessions and free courses are great opportunity to meet up with like-minded peers and enjoy
the opportunity of consulting an expert in the field.
Save Your Priceless Time and Efforts
Bakkah offers all what you need in one place
Customer Testimonials
Our learners are the reason we pursue this noble coaching mission!
We’ve accompanied our learners all the way during their learning process until they achieved their goal. Every now and then we receive a grateful comment from a previous learner/client praising the professionality of the trainer, course and the material provided during the sessions.